The push of a button now has the power to fulfill not just basic tasks, but also our most cherished wishes. Some deliver the latest smartphone, a pair of jeans, and even chairs in a day. Others deliver delicious meals in minutes.
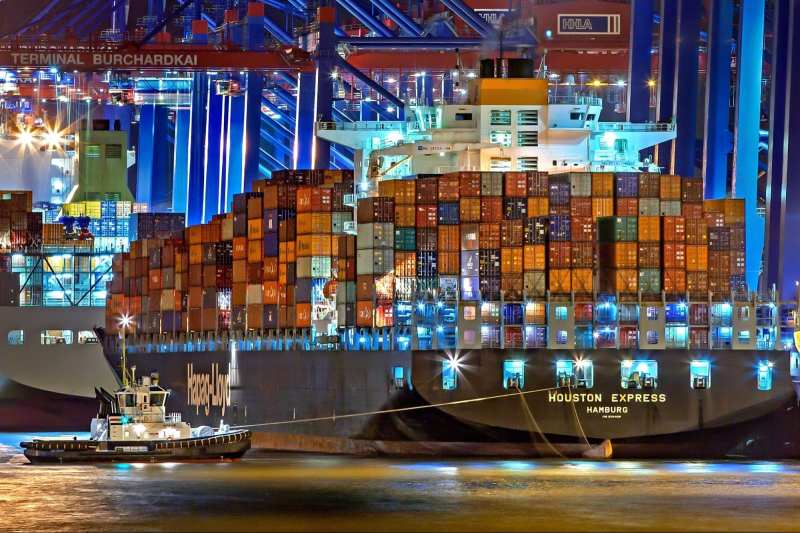
This convenience has not appeared overnight. Years of painstaking efforts by technology companies have helped make deliveries faster and less expensive. Take a look at Amazon: It has spent the better part of two decades reducing the delivery times of its US-based delivery services from eight days in the 2000s to one day in 2019.
That's a 75 per cent drop, and apart from low prices, it continues to set the benchmark for what makes for a delightful customer experience at the last mile. People now expect their orders to be delivered within hours (more increasingly, within minutes). Research has also shown that more than half of the consumers in the US are willing to switch brands if delivery times are too long. Something that consumers across the globe can relate to.
While the expectations are steep, it goes to show that the true opportunity to be remembered and valued by customers is at the logistics front, particularly at the last mile.
Taking on a mammoth task with technology
Many things need to go right for a delivery to be made on time in the last mile. Packages must also change several hands from the warehouse to a customer's doorstep—sort of like a baton in a relay race.
There is also the matter of scale. A lot of logistics planning boils down to finding the quickest possible route between two points. When you have two points, it is not much of an issue. Bump up that number to nine locations however, and you have a different story. The number of possible ways of traveling among these nine points equals the grains in 1 kg of sand. When you increase the number of locations to 22, the possibility of routes increases to the number of grains of sand in the entire universe.
As a company scales up, so does the number of orders, making technology indispensable to maintain the standard on on-time deliveries. Developments in artificial intelligence, machine learning, Internet-of-Things, Big Data analytics, among others, have now made it possible to create an entire logistics ecosystem that reduces costs and unlocks efficiencies at scale. Logistics companies rely on two functions to make it happen—automation and insights. These key capabilities include:
Geocoding: The process of converting fuzzy addresses into unique latitude and longitude coordinates, so that drivers do not spend too much time searching for the right location.
Fulfillment automation: Covers the automation of key fulfillment processes, including order capture, order allocation to vehicles, on the basis of real-life constraints, and tracking and updating of their status in real-time.
Slot management: Particularly useful for home service companies, it automates the assignment of tasks to drivers and skilled professionals based on consumer choice.
Route planning: Automation of finding the optimal route for a driver to make a set of deliveries, often on the basis of several real-life constraints such as distance, traffic, road blocks, fuel consumption, service level agreements (SLAs) etc.
Control Tower: An application that helps monitor the status of orders and carriers in real-time, and inform of any potential SLA breaches through automated alerts.
Tracking pages: That allow the end customer to receive real-time notifications on the status of their order.
Business insights: Applications that can analyze terabytes of data to show hidden inefficiencies, and growth opportunities through intuitive charts and auto-generated reports.
The age of the platform
Convenience is not something solely prized by end-customers. Logistics players need a seamless experience while juggling multiple products in order to be efficient. This means reducing the need for repetitive manual tasks, ensuring complete synchronization between new products and those that are already onboarded, streamlining notifications and alerts, and improving the visibility of operations by consolidating multiple views. Products also needed all relevant data to be standardized and have high fidelity across the board. In short: they all needed to have the same source of truth.
Bypassing the friction of the entire product procurement process to have things up and running in weeks, and not months is also highly valued. This is why logistics companies are moving towards offering their product range not in the form of a platform, and not individual solutions. A platform-based ecosystem allows logistics companies to use solutions in a plug-and-play manner. They can activate solutions as and when they need to in smaller time frames. Such solutions are also being made available in the form of Application Programming Interfaces (APIs) that can be easily integrated with existing Enterprise Resource Planning (ERP) software.
A win-win situation
The sustainable growth of India's logistics industry is paramount to the success of many industries and sectors. Logistics companies continue to provide innovative solutions that reduce costs, bring efficiencies at scale, and meet the demands of a rapidly changing business world.